Stop! Machine Guards
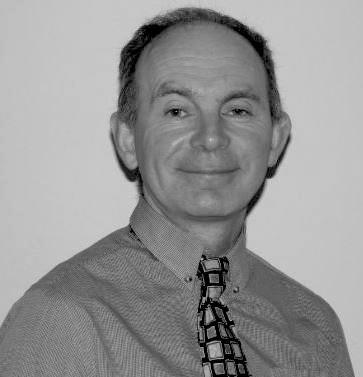
TONY MANGAN
Health and Safety Consultant
EazySAFE
Crushed fingers, broken bones, amputation, strike by flying material. These are just some of the real outcomes of poorly guarded machines. It can be life altering. And it can kill. Each piece of machinery has its own unique mechanical and non-mechanical hazards, causing injuries from minor to very severe. Each machine must have adequate safeguards to protect operators and other employees in the immediate work area from hazards created by ingoing nip points, rotating parts, sparks, splashes and flying debris.
When looking at how to guard machines, ask yourself these seven questions:
- What are the requirements?
- Where do I position them?
- How do I attach them?
- How far from the danger zone?
- What are the design requirements?
- What material?
- Can they be by-passed?
Note that guards must be:
- Of robust construction
- Not give rise to any additional risk
- Difficult to by-pass
- Be located at an adequate distance from the danger zone
- Cause minimum obstruction to the view of the production process
- Foreseeable abuse and normal wear and tear must be taken into account in the design
- Enable essential maintenance work to be carried out on installations and/or replacement of tools and also only to be the area where work has to be done, of possible without the guard or the protection device having to be dismantled
There are four types of machine guarding:
- Fixed
- Movable
- Adjustable
- Protective devices
1. Fixed Guards
Fixed guards are a permanent part of the machine. They can only be removed using a tool. They are the preferred type of guard as they are relatively simple. They can provide maximum protection. However, they may interfere with visibility and if machine adjustments and repair need to be done, they must be removed and other means of protection is needed.
2. Moveable Guards
These guards are fixed guards that can be moved out of position but not detached from the machine.
When this type of guard is opened or removed, the tripping mechanism and/or power automatically shots off or disengages, the moving parts of the machine are stopped, and the machine cannot cycle or be started until the guard is back in place. Replacing the guard must not automatically restart the machine. All removable guards should be interlocked to prevent occupational hazard.
Advantages of this type of guard are that they can provide maximum protection and allow access to the machine for removing jams without time consuming removal of the fixed guard. However, moveable guards require careful adjustment and maintenance and may be easily disengaged.
3. Adjustable Guards
These guards may be moved or configured to allow for different types of production, such as different sizes of stock or raw materials. They should be designed to reduce as far as possible the risk of ejection. However, hands may enter the danger area as protection may not be complete at all times, the guard may be made ineffective by the operator, and they may interfere with visibility.
4. Protective Devices
Protective devices are also known as safety components. They must be CE compliant.
Examples of such devices include:
- Interlocks
- Two-handed controls
- Light curtains
- Pressure mats
Interlock (Switch)
These switches shut off or disengage the power whenever e.e. the door is opened or pushed out of position. They are connected to the movable guard so that when it is opened, the machine stops. Examples include washing machines and microwaves
Two Handed Controls
Two-handed controls are used when it is necessary for the operator to keep their hands clear of the danger zone (e.g. punch press). It forces the operator to use both hands to operate the machine controls. They should be spaced well apart. The machine should only operate when both controls are activated together.
These safety components are only of use to the operator and do not safe guard third parties. They should only be used in conjunction with other guarding types, e.g. three-sided enclosure, the open side being directly in front of the operator.
Light Curtains
This is an electro-sensitive optical device used to protect people working near dangerous machines. When the light curtain senses entry into the protected zone by an object, it sends a stop signal to the machine. Light curtains are generally used when the operator requires frequent access and in doing so is exposed to a risk (crushing, entanglement etc.). Light curtains can replace mechanical guards if the operating environment is not polluted (splashing, splattering, dusty etc.)
Pressure Sensitive Mats
These are designed to detect the presence of people on its sensing surface. If someone or something is on the mat, the machine will not start. When the machine is operating, it will stop if someone steps on the mat.
So, what do you do?
Conduct a risk assessment. Where hazards are identified, use the “Hierarchy of Control” to determine the best course of action.
If you cannot eliminate, substitute or isolate the hazard, guarding, which is a form of Engineering Control may be the best solution.
Ask yourself the seven questions, and see what guarding is best suited.
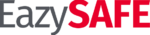
Discover our Safety Training Platform
Train your employees anytime, anywhere with our environmental, health, safety and wellness training platform.
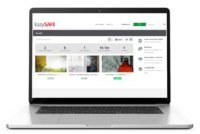
TAILORED TRAINING
Discover our safety training courses and ehs onboardings, which can be customised and offered in several languages.
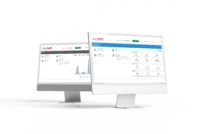
SAFETY MANAGEMENT
Ensure the distribution of your safety policy by training your permanent, temporary or seasonal staff.
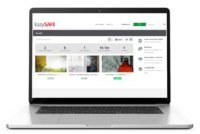
GLOBAL MONITORING
Simplify the management of your safety policy thanks to the numerous dashboards and training reports.